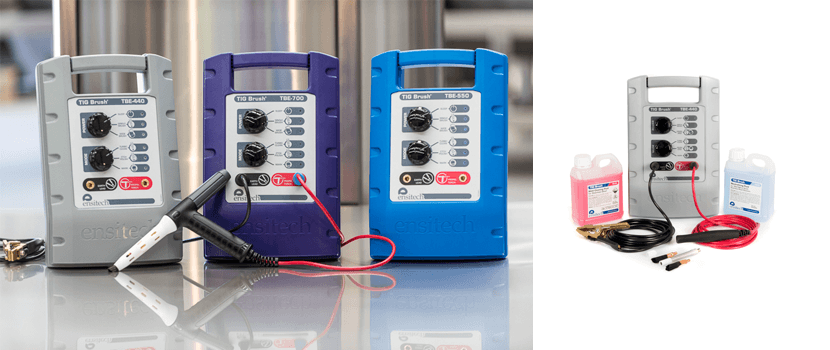
Weld cleaning is a critical step in the fabrication process, ensuring the removal of oxides, scales, and discoloration from welded surfaces. Traditionally, this process involved labor-intensive methods that were time-consuming and often produced inconsistent results. However, with the advent of advanced technology, the Tig Brush has emerged as a revolutionary tool, challenging conventional methods and setting new standards in weld cleaning.
In the dynamic world of welding technology, the TIG Brush weld cleaning machine has emerged as a game-changer, revolutionizing the post-weld surface treatment process. Here’s a closer look at the significance and advantages of TIG Brush weld cleaning machines:
1. Efficient Removal of Heat Tints:
- TIG Brush machines efficiently remove heat tints, oxidation, and discoloration from welded surfaces. This is critical in maintaining the aesthetic appearance of stainless steel and other alloys.
2. Enhanced Corrosion Resistance:
- By eliminating oxides and contaminants, TIG Brush weld cleaning enhances the corrosion resistance of stainless steel welds. This is particularly crucial in applications where the material’s longevity is paramount.
3. Consistent Finishes:
- TIG Brush technology ensures consistent surface finishes, meeting quality standards and specifications. The uniform appearance achieved contributes to the overall visual appeal of the welded components.
4. Versatility in Material Compatibility:
- TIG Brush machines are versatile and compatible with various materials, including stainless steel, aluminum, and other alloys. This versatility makes them suitable for a wide range of welding applications.
5. Time and Labor Savings:
- Traditional methods of post-weld cleaning often involve manual labor and extensive time. TIG Brush weld cleaning machines automate and expedite the process, resulting in significant time and labor savings.
6. Environmentally Friendly:
- TIG Brush technology employs safe and eco-friendly processes, using a combination of low-toxicity fluids and electrical power. This aligns with modern sustainability practices, making it an environmentally responsible choice.
7. Reduced Consumable Costs:
- TIG Brush machines reduce the reliance on consumables such as brushes and abrasives. The system’s longevity and minimal consumable usage contribute to cost savings over time.
8. Enhanced Safety:
- The automated nature of TIG Brush weld cleaning minimizes the need for manual labor in potentially hazardous environments. This enhances overall safety standards in welding operations.
9. Improved Consistency:
- Automation ensures a consistent and repeatable cleaning process across various welds. This consistency is crucial for meeting quality control standards and ensuring the reliability of welded components.
10. Suitability for Various Welding Applications:
- TIG Brush weld cleaning is applicable in diverse welding scenarios, including pipe welding, structural fabrication, aerospace, automotive, and more. Its adaptability makes it a valuable tool in different industries.
11. User-Friendly Operation:
- TIG Brush machines are designed with user-friendly interfaces, making them accessible to operators with varying levels of experience. The simplicity of operation contributes to their widespread adoption.
The Tig Brush, a versatile tool in the realm of welding, finds applications across various industries, providing efficient and effective solutions for weld cleaning and surface preparation. Here are some key applications of the Tig Brush:
1. Stainless Steel Weld Cleaning:
- The Tig Brush is particularly well-suited for cleaning and passivating stainless steel welds. It efficiently removes heat tint, scale, and discoloration, leaving behind a clean, corrosion-resistant surface.
2. Aluminum Weld Cleaning:
- Aluminum welding often results in oxide layers that need to be removed for optimal performance. The Tig Brush’s electrochemical cleaning process is gentle on aluminum surfaces, ensuring a clean finish without abrasion.
3. Weld Passivation:
- After welding, especially in stainless steel applications, passivation is crucial to enhance corrosion resistance. The Tig Brush simplifies the passivation process, promoting the formation of a protective oxide layer.
4. Food and Pharmaceutical Industries:
- Industries with stringent hygiene standards, such as food and pharmaceuticals, benefit from the Tig Brush’s ability to clean welds without introducing contaminants. It ensures compliance with industry regulations.
5. Architectural Welding:
- Weld aesthetics are vital in architectural applications. The Tig Brush provides a consistent and uniform finish, enhancing the visual appeal of welded structures in architectural designs.
6. Automotive Welding:
- In automotive manufacturing, where precision and efficiency are paramount, the Tig Brush offers a faster and more reliable solution for weld cleaning, contributing to streamlined production processes.
7. Aerospace Industry:
- The aerospace sector demands high-quality welds with minimal surface imperfections. The Tig Brush’s ability to deliver a uniform finish makes it a valuable tool in aerospace welding applications.
8. Medical Device Manufacturing:
- The medical industry requires precise and clean welds, especially in the manufacturing of medical devices. The Tig Brush ensures the removal of contaminants without compromising the integrity of the weld.
9. Maintenance and Repair:
- The Tig Brush is not limited to new welds; it is also employed in maintenance and repair tasks. It efficiently cleans and restores the appearance of existing welds.
10. General Fabrication:
- Across various fabrication projects, the Tig Brush’s versatility shines. It addresses the common challenges associated with weld cleaning, making it a valuable asset in general fabrication processes.
The Tig Brush’s adaptability, speed, and environmentally friendly approach position it as a go-to solution for weld cleaning in diverse industries. Whether it’s achieving a polished finish on architectural elements or ensuring the longevity of stainless steel components in harsh environments, the Tig Brush proves its effectiveness across a spectrum of applications.
The Tig Brush has undoubtedly revolutionized weld cleaning by offering a safer, more efficient, and environmentally friendly alternative to conventional methods. As industries continue to prioritize quality, efficiency, and safety, the Tig Brush stands out as a transformative tool, setting a new standard in the world of weld cleaning. Embracing this advanced technology not only enhances the overall welding process but also contributes to a sustainable and safer work environment.
Aerospace Industry:
- In the aerospace sector, where lightweight materials such as aluminum and titanium are prevalent, TIG welding is preferred for its ability to produce strong, precise welds without compromising the integrity of the materials.
Automotive Manufacturing:
- TIG welding is widely used in the automotive industry for welding components that demand high strength and durability. It’s particularly suitable for applications involving thin materials and critical joints.
Stainless Steel Fabrication:
- TIG welding excels in welding stainless steel, offering excellent control over the heat input. This is crucial for preventing distortion and maintaining the corrosion resistance of stainless steel components.
Pipe Welding:
- TIG welding is commonly employed in pipe welding, especially for industries such as petrochemicals and oil and gas. Its ability to produce clean and precise welds makes it suitable for critical piping systems.
Nuclear Industry:
- The nuclear industry demands high-quality welds to ensure the structural integrity of components. TIG welding, with its ability to create strong and defect-free welds, is widely used in nuclear applications.
Medical Device Manufacturing:
- TIG welding is crucial in the production of medical devices, where precision and cleanliness are essential. It allows for the welding of small and delicate components without compromising their functionality.
Food and Beverage Industry:
- The food and beverage industry requires hygienic welding practices. TIG welding’s ability to create clean and smooth welds without the need for filler material makes it suitable for stainless steel components in this industry.
Artistic Welding:
- TIG welding is favored in artistic applications due to its precise control. Artists and sculptors use TIG welding to create intricate metal sculptures and structures.
High-Performance Alloys:
- TIG welding is compatible with a wide range of materials, including high-performance alloys. This versatility makes it a preferred choice in industries working with diverse materials.
Welding Thin Materials:
- TIG welding’s low heat input and precise control make it suitable for welding thin materials, minimizing the risk of distortion and ensuring a clean finish.
In the realm of weld cleaning, the Tig Brush Cleaning Machine in UAE has emerged as a transformative force, challenging and surpassing conventional methods. Let’s delve into the comparison between Tig Brush technology and traditional approaches to post-weld surface treatment.
1. Efficiency and Speed:
- Tig Brush:
Utilizes an automated process, swiftly removing heat tints and contaminants.
Achieves faster results, reducing the time spent on post-weld cleaning.
- Conventional Methods:
Often involves manual labor, leading to a slower and more labor-intensive process.
2. Consistency in Results:
- Tig Brush:
Ensures uniform surface finishes across welds, meeting quality standards.
- Conventional Methods:
Manual techniques may result in uneven cleaning, impacting the overall appearance.
3. Material Compatibility:
- Tig Brush:
Versatile and compatible with various materials, including stainless steel and aluminum.
- Conventional Methods:
May require different approaches for different materials, complicating the process.
4. Environmental Impact:
- Tig Brush:
Implements eco-friendly processes with low-toxicity fluids and minimal waste.
- Conventional Methods:
May involve the use of harsh chemicals, contributing to environmental concerns.
5. Labor Savings:
- Tig Brush:
Reduces dependence on manual labor, resulting in significant time and cost savings.
- Conventional Methods:
Relies heavily on manual effort, potentially increasing labor costs.
6. Consistent Safety Standards:
- Tig Brush:
Minimizes manual involvement, enhancing safety in welding environments.
- Conventional Methods:
Manual labor poses potential safety risks in hazardous welding conditions.
7. Consumable Usage:
- Tig Brush:
Reduces the need for consumables such as brushes and abrasives.
- Conventional Methods:
May require frequent replacement of consumables, contributing to additional costs.
8. Ease of Operation:
- Tig Brush:
Designed with user-friendly interfaces, making it accessible to operators of varying expertise.
- Conventional Methods:
Manual techniques may require skilled operators for effective results.
9. Application Flexibility:
- Tig Brush:
Applicable in various welding scenarios, from pipes to structural fabrication.
- Conventional Methods:
May be less adaptable to diverse welding applications.
10. Long-Term Cost Savings:
- Tig Brush:
Offers longevity and reduced consumable costs over time.
- Conventional Methods:
Consumable usage and labor-intensive processes may result in higher overall costs.
Tig Brush’s automated and efficient approach to weld cleaning has redefined industry standards, outperforming conventional methods in terms of speed, consistency, and environmental impact. As industries prioritize efficiency, cost-effectiveness, and safety, Tig Brush technology stands out as a progressive and indispensable solution in the realm of weld cleaning.
To know more about Applications of Laser Engraving & Cutting Machines in the UAE