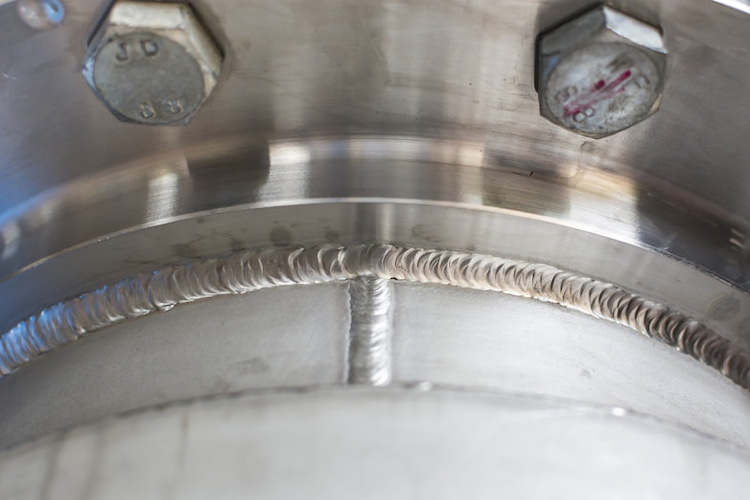
Weld cleaning machines made of stainless steel have become a standard piece of equipment in the collection of modern fabricators. Manufacturers are aware of the unique benefits these devices offer over the conventional, dangerous way of passivating surfaces using pickling paste. Even though this technology is still in its beginnings, some end-users continue to have concerns about its potential. You might believe you are witnessing a magic performance if you have never seen one of these instruments in operation. You can be confident that the final product will guarantee that the manufacturer’s longevity and skill will be well-known in years to come, which will result in additional business coming in.
If your stainless steel looks dull, cloudy, or has a matte finish after using an electrolytic cleaner, you might have a machine that’s not doing a good job. A great electrochemical weld cleaner should leave the stainless steel with a very smooth and super clean surface. Even though electro cleaning doesn’t scratch or polish the surface, a good European machine should have a polishing feature to make it look even smoother and shinier when needed.
There are three well-known ways to get rid of colors caused by annealing on a stainless steel TIG weld:
- The chemical way, which uses a strong cleaning liquid made of hydrofluoric, nitric, and sulfuric acid.
- The mechanical way, where you manually brush it, like using a stainless-steel wire brush, or spinning plastic brushes or soft cloths.
- The electrochemical way, which uses electricity and a special fluid.
High-quality weld cleaners for stainless steel are significantly more than simple cleansers. They may be used to polish stainless steel to a mirror shine according to their many operating modes. If your surface has previously been unclean, used, or damaged, this is perfect for you.
Additionally, these devices can ‘print’ or ‘engrave’ your own branding on the surface. This is a great way for builders to show their work to possible customers. You can make different sizes and patterns, like a unique number, or stronger ones that stay good for a long time based on how you take care of them.
Cleaning solutions and brushes do not last long, and getting replacements can be expensive.
These weld cleaning machines have the same goal, but they give different results. It’s like expecting a Prius car to perform like a Ferrari – they’re not the same. So, instead of going for the most expensive machine, it’s better to be practical and choose one that fits the job’s needs.
Some machines start with a lower cost but end up being more expensive because they use a lot of cleaning liquid and need more replacement parts. They have a pump that uses more cleaning fluid than necessary. This can create a mess and cost you extra money. A good machine lets you dip the brush into the liquid, so you only use what you need, reducing waste and giving better results.
Usually, you need about 2 liters of cleaning fluid to clean around 150 meters of a weld. Here’s how long the brushes usually last:
- For TIG welds: 60-80 hours
- For MIG welds: 55-65 hours
- For Stick welds: 40-50 hours
This is an important point to think about. Many machines in the market show how well they clean a clean TIG weld, but let’s be honest, any good weld cleaner can do that. But what about in real life, where you might have MIG welds that got very hot and turned blue or purple? Well, it’s not just about the power (amperage) of the machine. It’s more about whether the machine can handle tougher jobs like these. Cheaper options often fail in this area. It depends on the technology inside the machine and whether it can perform well when it’s working hard. You might need to change settings to get the best result, and sometimes it still won’t work as it should.
Stainless steel welds can also be cleaned using tools like stainless steel wire brushes, spinning plastic brushes on drills, or non-woven cloth. It’s a physical job, and one advantage is that these tools don’t cost much.
But, cleaning with brushes or cloth takes a lot of time. Plus, if the person doing the cleaning is not skilled, they might accidentally make scratches on the TIG welds and the base material. The big problem with this method is that not every spot can be reached, so there is still a chance of corrosion happening.
Using Electrochemical Weld Cleaners for Stainless Steel Welds
Weld cleaners are special devices that clean stainless steel welds well and fast. To do this, you need a special cleaning liquid called an electrolyte, and you also need a regular electric current, like the kind you have in your home, in addition to the weld cleaner. You just put the electrolyte on the TIG welds or the stainless steel that needs cleaning.
Here’s how it works: The part with the weld that needs cleaning is connected to the weld cleaner with a cable. Then, you use a cleaning pad or a special brush, and you move it over the weld while it’s wet with the electrolyte. Most of the cleaning happens because of the electric current, which goes back and forth, like a see-saw, between being positive and negative. This gets rid of the colors from the welding without hurting the stainless steel’s surface.
And, when the electrolyte evaporates, it makes oxygen. This oxygen sticks to the chromium in the stainless steel, making a protective layer. This layer makes sure the stainless-steel stays looking good. The cleaning and the making of the protective layer happen at the same time, so you do not have to wait for it to happen on its own, like you do with other cleaning methods.
Using High Heat for Welding or Cutting Stainless Steel
Heat is important when you’re working with Stainless steel weld cleaning machine in UAE. But, if there’s too much heat when you’re welding or cutting, it can create issues. Stainless steel is thinner than regular steel, so too much heat can make it even thinner and weaker.
This means the metal might change its shape and bend, which means the workers have to either start all over with a new piece of stainless steel or spend time fixing the metal to make it right again.
Usually, the companies that make these machines use a cleaning solution that has phosphoric acid in it. When you clean with this solution, it gets warm, and you might see some steam coming up from the surface. Most of what you see is steam, about 90%, and it’s much safer than the fumes that come from welding. The important thing is to use the right safety gear. A good-quality weld cleaning machine will come with a special mask called a P2 mask, and it has a filter that’s safe for the environment. You should also wear safety glasses to protect your eyes and nitrile gloves to keep your hands safe. This gear is enough to keep you safe all day.
Find out more about How To Choose The Right Laser Cutting Machine in UAE?